DATE
16th April 2025
CATEGORY
Artificial Intelligence, Manufacturing
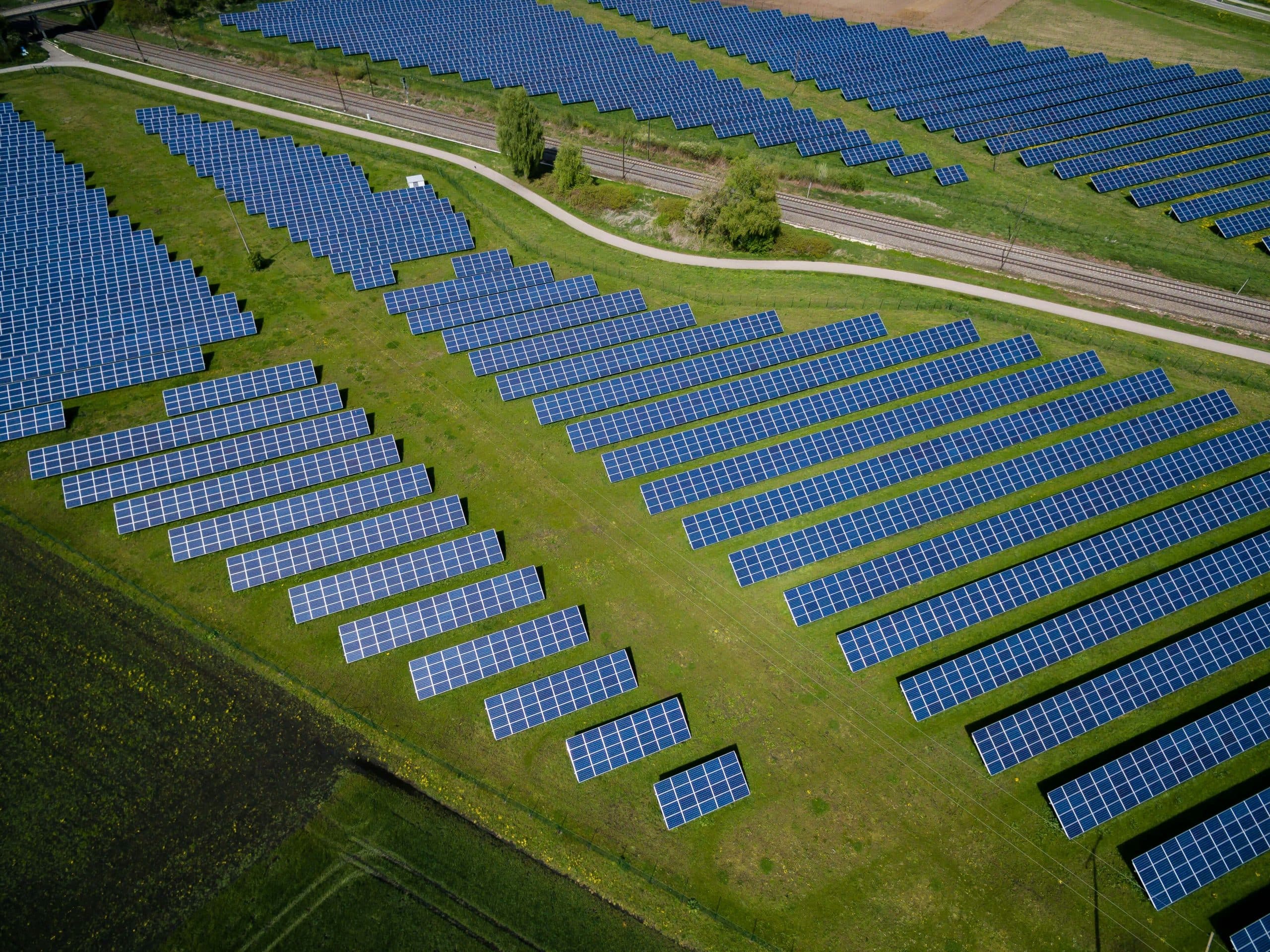
Introduction to Energy Consumption in Manufacturing
In the manufacturing sector, energy consumption is a significant operational expense. It not only impacts the bottom line but also sets the tone for the sustainability practices within the business. With rising energy prices, the ability to manage and optimize energy consumption has become crucial for enhancing operational efficiency.
Managing energy effectively can lead to significant cost savings. In fact, manufacturers that focus on energy efficiency have been shown to reduce costs by up to 20%. Furthermore, sustainable energy management is more than just a buzzword; it’s a necessity for compliance as regulatory bodies push for greener practices. Achieving compliance not only helps in avoiding penalties but also positions your brand favorably in the market.
The Challenges of Energy Management in Manufacturing
Despite the clear benefits, many manufacturing companies struggle with traditional energy management practices. Common inefficiencies include outdated equipment, lack of real-time energy data, and a reactive approach to energy usage rather than a proactive strategy.
The complexity of energy consumption data can overwhelm operations in large production facilities. Often, data is scattered across multiple systems, making it difficult to get a comprehensive view of energy usage. This fragmentation leads to challenges in identifying patterns and anomalies, which can significantly drive up costs.
Aligning energy management strategies with production goals poses another hurdle. When energy management isn’t integrated with production processes, inefficiencies can arise, ultimately impacting both energy costs and production output.
How AI Solutions Can Optimize Energy Consumption
AI offers powerful solutions to optimize energy consumption in manufacturing. One of the most impactful applications is the use of predictive analytics. By forecasting energy needs based on historical data and production schedules, manufacturers can make informed decisions about energy usage and reduce waste.
Additionally, real-time monitoring and reporting of energy consumption patterns allow companies to respond swiftly to changes, helping prevent energy waste. Automated energy optimization strategies can adjust energy consumption dynamically in response to production fluctuations, thereby enhancing efficiency.
IoT devices integrate seamlessly with AI, enhancing data collection and analysis. For instance, smart sensors can detect when machinery is not in use, prompting systems to reduce energy input automatically, leading to further savings.
Case Studies: Successful Implementation of AI in Energy Management
A notable example involves a manufacturing company that achieved a remarkable reduction in energy costs by 30% through the implementation of AI-driven energy management systems. Utilizing forecasting models allowed them to adjust energy consumption effectively according to production needs.
Moreover, a case study on predictive maintenance highlighted how a company improved energy efficiency by utilizing AI for monitoring equipment health. This proactive approach minimized downtime and reduced energy waste associated with faulty machines.
AI-driven energy models were crucial in helping another organization meet its sustainability goals. They successfully aligned energy management with their broader corporate social responsibility (CSR) initiatives, demonstrating that energy efficiency can coincide with environmental stewardship.
However, not all initiatives are successful. Learning from failures in energy management automation projects can provide valuable insights into the common pitfalls and help in crafting more successful strategies.
Best Practices for Implementing AI in Energy Optimization
To effectively implement AI solutions for energy optimization, it’s essential to establish clear energy consumption goals and key performance indicators (KPIs). This transparency not only helps in tracking progress but also unites the team around common objectives.
Investing in staff training on AI tools and technologies is vital for maximizing the benefits of these systems. An informed team will be more adept at leveraging AI to drive energy optimization.
Collaboration with AI solution providers can also enhance outcomes. Tailored implementations align the technology with specific operational needs, driving more significant results.
Lastly, continually evaluating and adapting your energy management strategy based on real-time data is crucial for long-term success. Flexibility and responsiveness to changing conditions will keep your energy management ahead of the curve.
Future Trends: The Evolution of AI in Manufacturing Energy Efficiency
Looking ahead, emerging AI technologies, such as advanced machine learning algorithms, promise to transform energy management even further. These innovations will facilitate continuous improvement by enabling systems to learn from new data and optimize proactively.
Predictions also indicate upcoming regulatory changes that will influence energy consumption strategies, emphasizing the need for manufacturers to stay ahead of compliance requirements and technological advancements.
Fostering a corporate culture that embraces technological innovation will be paramount. By promoting an environment that supports pioneering energy management practices, companies can ensure they harness the full potential of AI solutions.
Conclusion: Taking the Next Steps Towards Energy Optimization
AI presents transformative potential for energy management in manufacturing, driving both efficiency and sustainability. It’s essential for executives to prioritize energy visibility within their operations, creating actionable insights that prompt significant cost savings.
For those looking to deepen their understanding, numerous resources are available that detail the interplay between AI and energy efficiency. Take action today—embark on your AI journey to optimize energy consumption and create a more sustainable future for your manufacturing operations.